Written by: Jaden Crute (B.S. Engineering Student)
Marine engineering isn’t typically something you would think of when imagining an engineer’s potential career path. Despite this, it makes a lot of sense that the fields of marine science and engineering overlap. I have always had a passion for marine science, but I was convinced that I had to choose one interest and stick with it. So, I went with Mechanical Engineering here at the University of South Florida. During my sophomore year, I was fortunate enough to stumble upon professors and advisors who introduced me to the amazing world of marine engineering. As I enter my final year of school, there isn’t a doubt in my mind that this is the field for me.
During my junior year, I was offered an internship with USF’s Center for Ocean Mapping and Innovative Technologies (COMIT) through a professor that I knew in the College of Marine Science (CMS) where COMIT is housed. I was given a few choices for a project to work on, but ultimately decided to work on an uncrewed surface vehicle (USV) now affectionately known as Trevor (Test Robotics Environment Vehicle for Ocean Research). The base of the vehicle was originally created several years ago for the Center for Ocean Technology (COT) at CMS, and my job was to repurpose it.
My first task was to make Trevor controllable with a Logitech controller. This required me to find an online user manual for the motor controller to figure out how to speak to it. Once I knew the syntax (or language) of commands the motor controller required, I then had to learn and write python code for the controls.
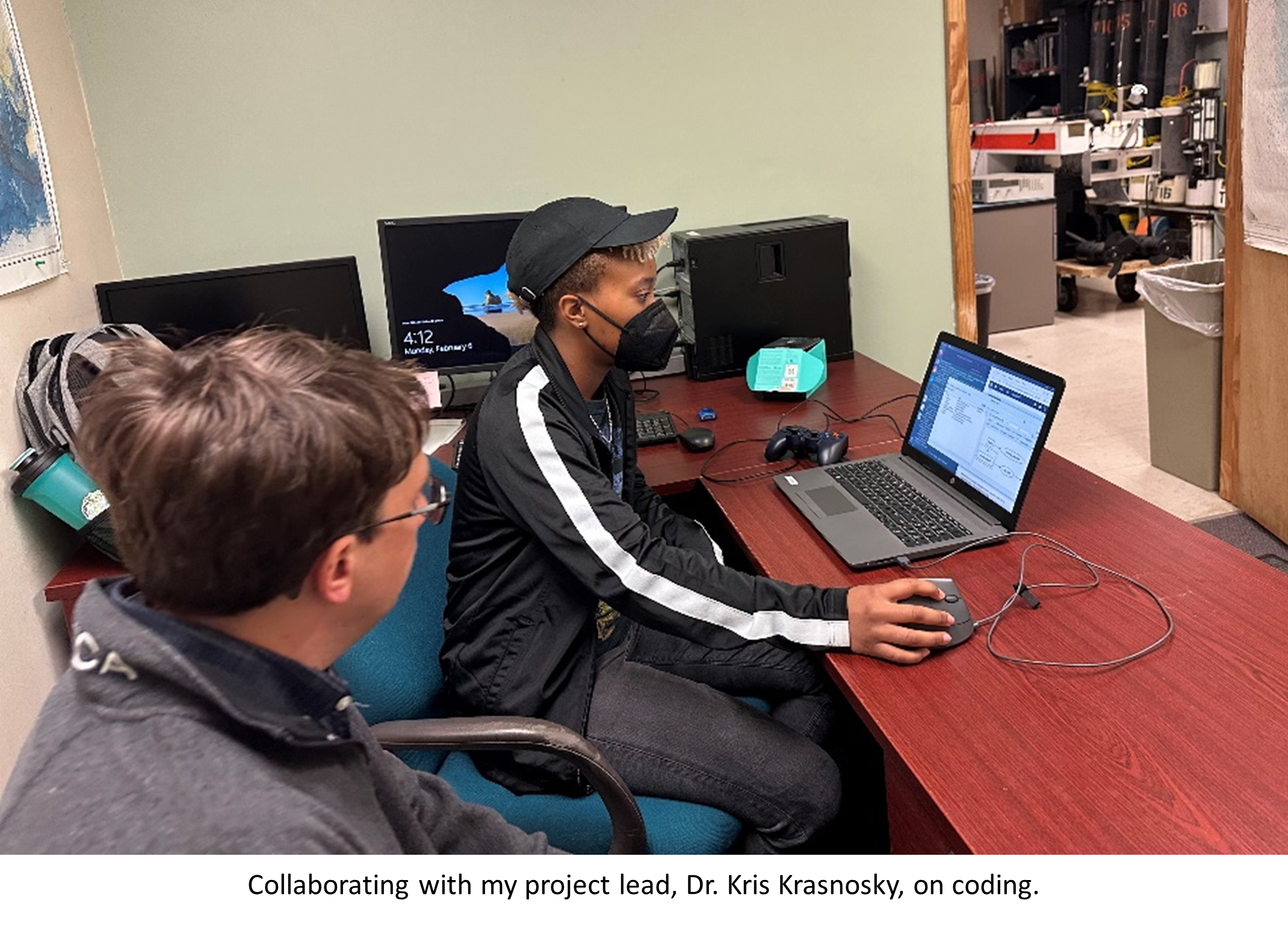
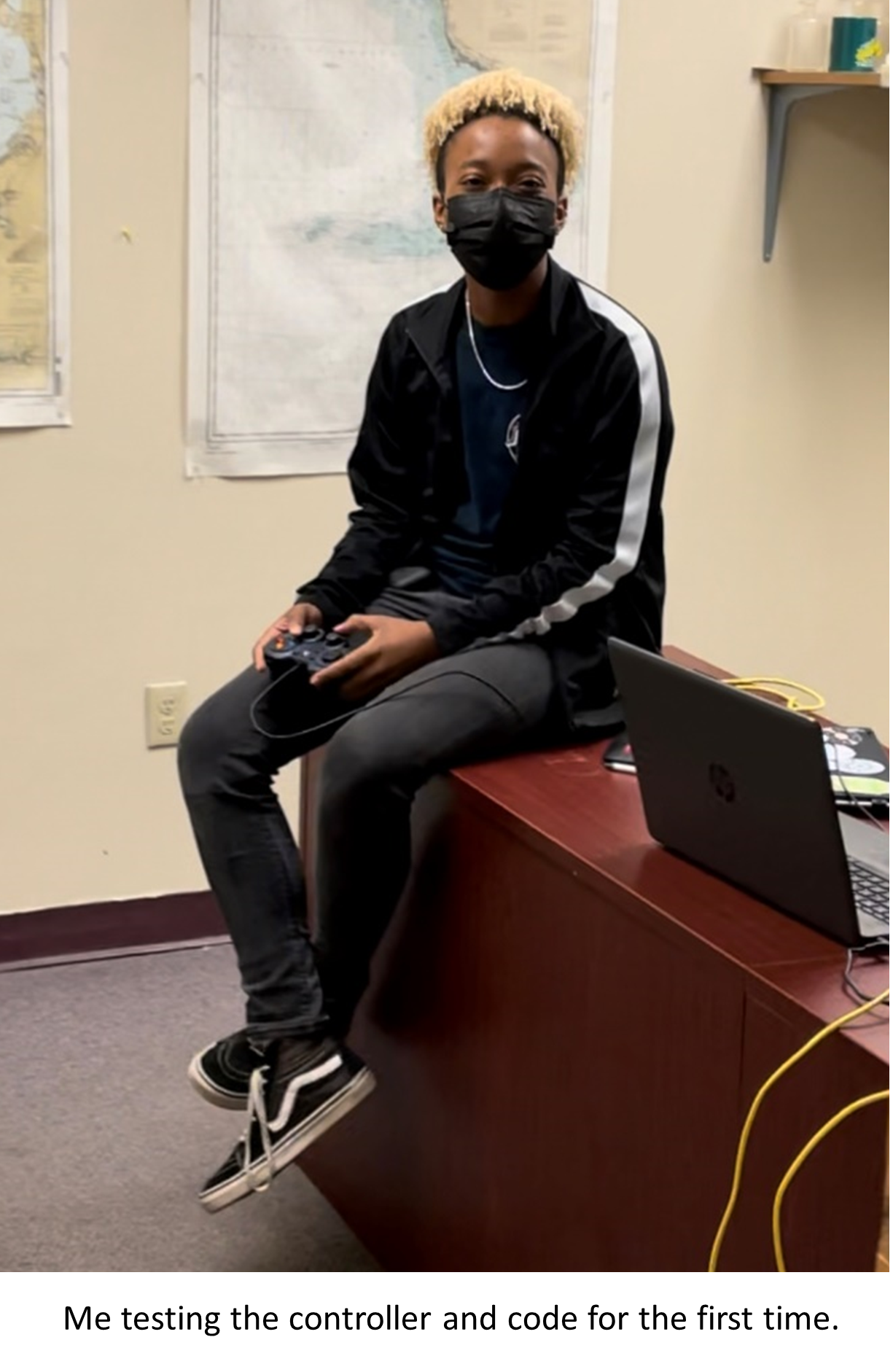
Once I had the controller up and running, we got to do the very first field test on the vehicle. The controller worked perfectly, and I was so proud that the work I was doing on the vehicle had visible results.


During the field test we found things that we wanted to improve to help with Trevor’s performance, the first of which had to do with increasing the pitch of the propeller blades. The pitch of a propeller is the theoretical distance that the propeller moves forward in one revolution of its blades. So as the pitch increases, performance tends to increase as well. Using the design software that I’m accustomed to on this portion of the project was a true test of my skills, but after consulting with TA’s and YouTube, I was able to get a working propeller design.
Next, I decided to resin print a test propeller to see how it held up. This is where things get interesting. This internship has taught me something very important about what it means to be an engineer. In almost all cases, engineering is about breaking things over and over again until they function as intended. You see, I got the vehicle set up in our indoor tank and gave it the slightest bit of power. As soon as the props started turning there was a loud cracking noise and I saw a piece of the propeller fly out of the water and onto the floor. I thought, maybe I just need to print a new propeller with increased thickness to increase its strength. The next propeller proceeded to break in the same way.
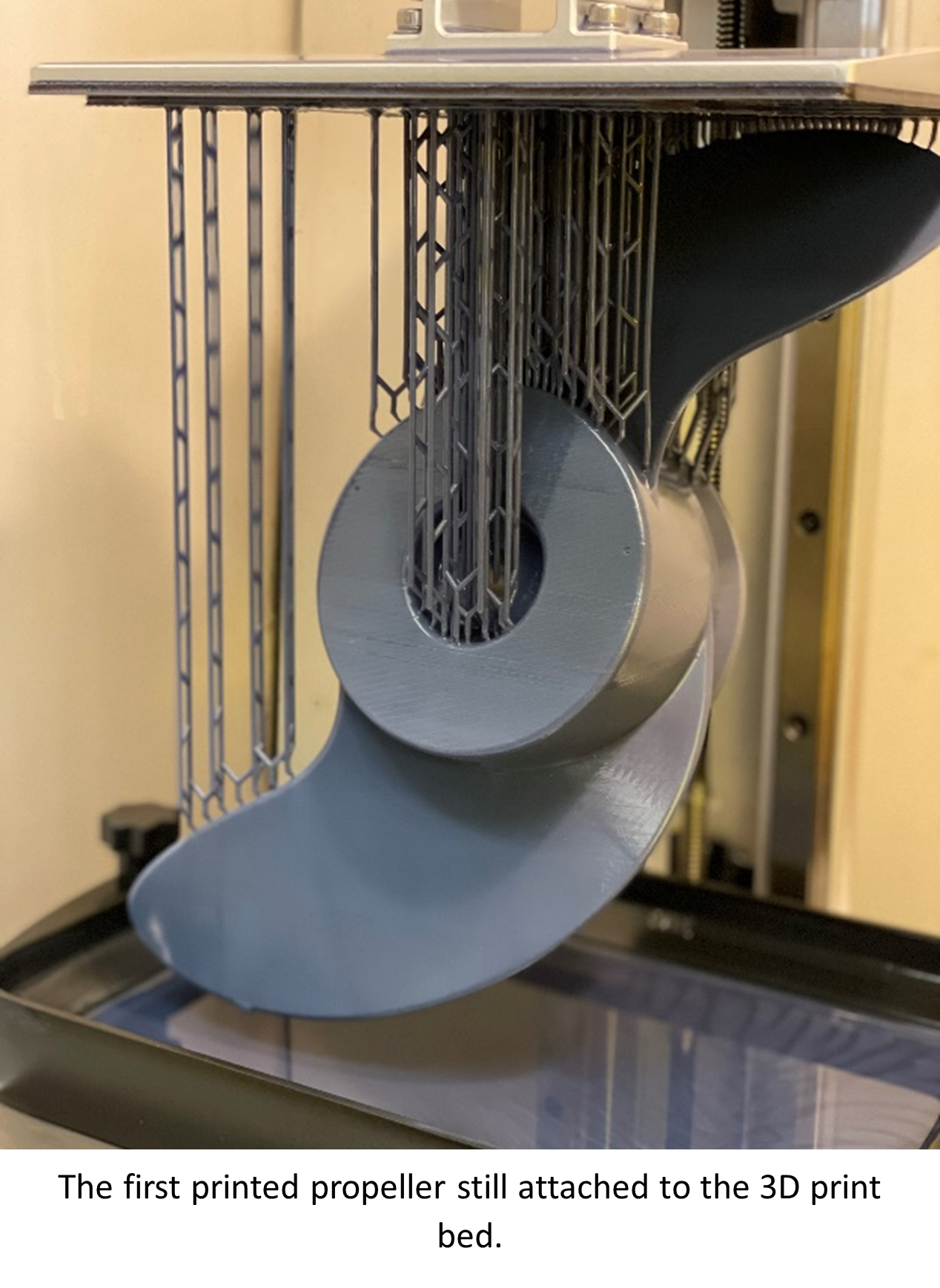
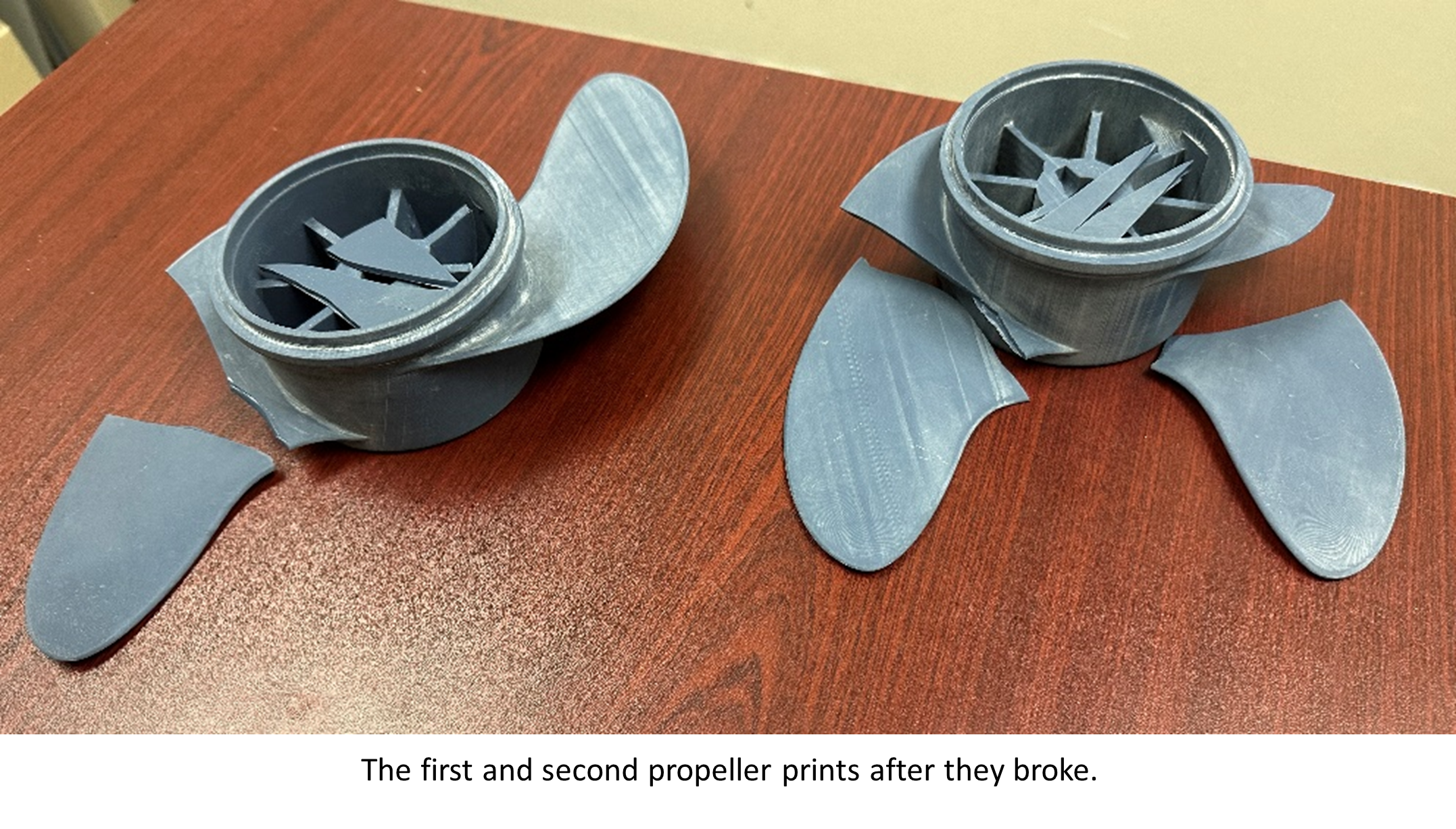
My next solution was to change to a more durable resin. I had done flex tests with the new resin to test its strength, so I was confident that it would hold up. We set up for yet another tank test and this time it held up to full throttle. So, I printed another propeller in preparation for a field test. At this point we also had new hulls that I had designed mounts for, so the field test was meant to evaluate both of these new features.
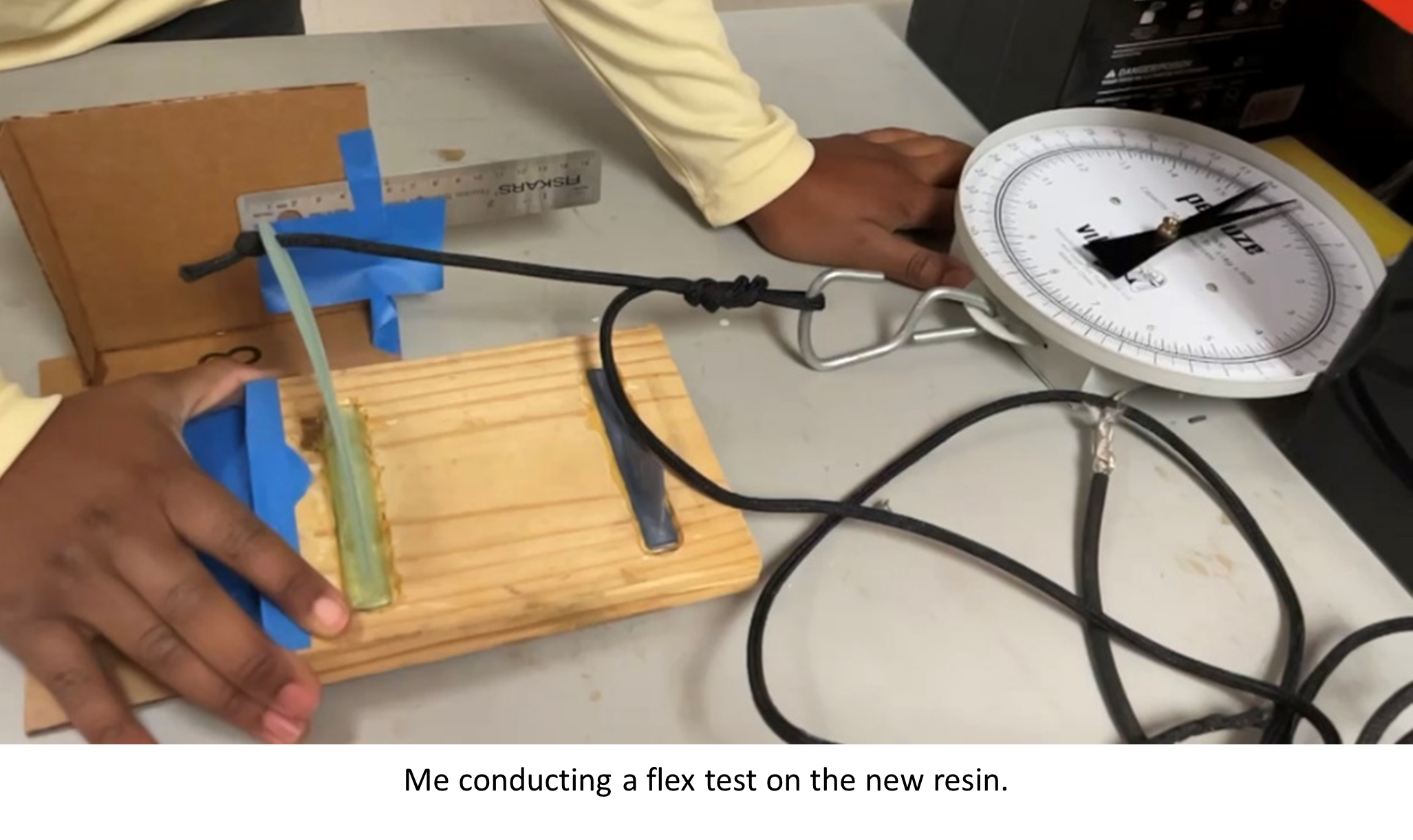
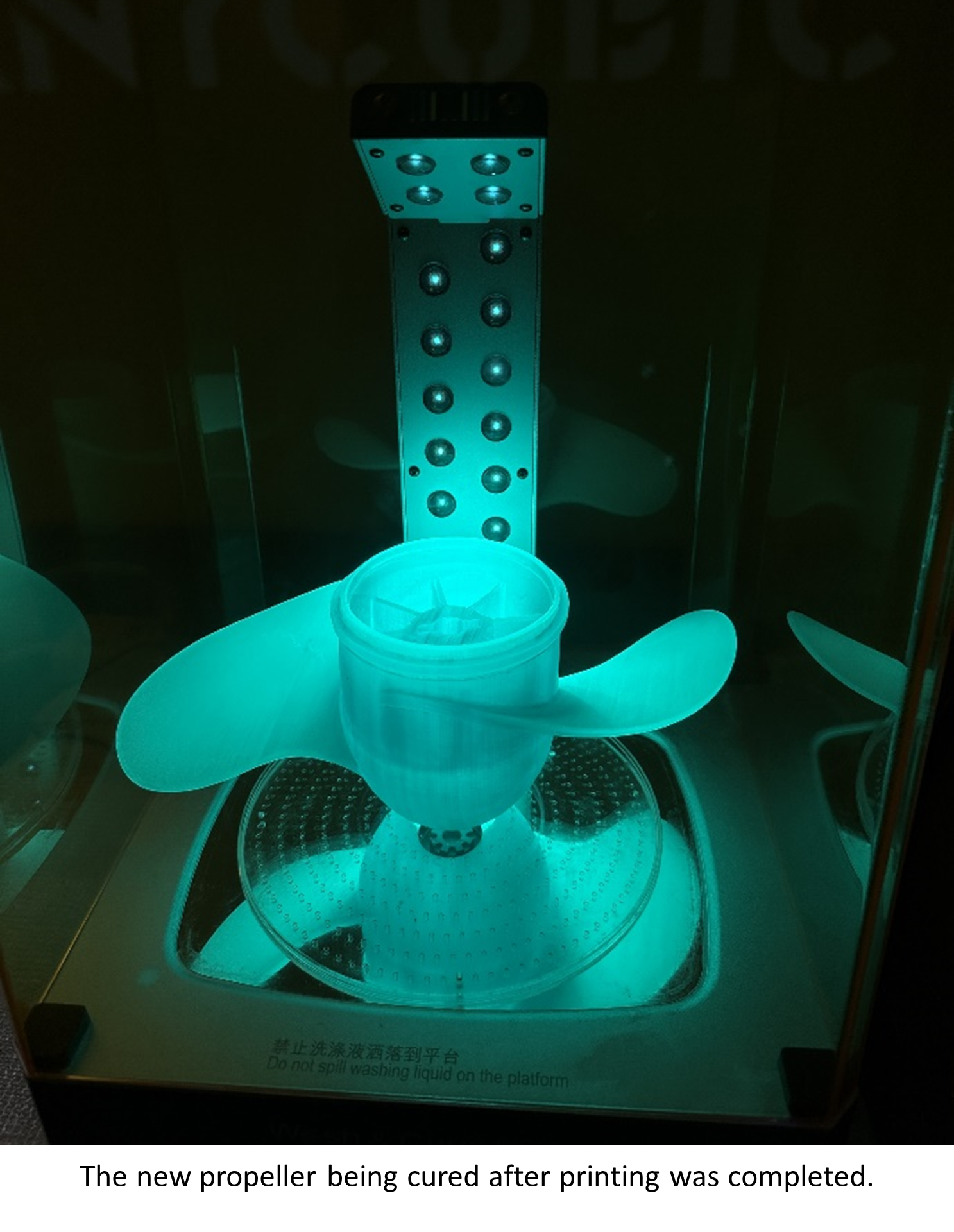
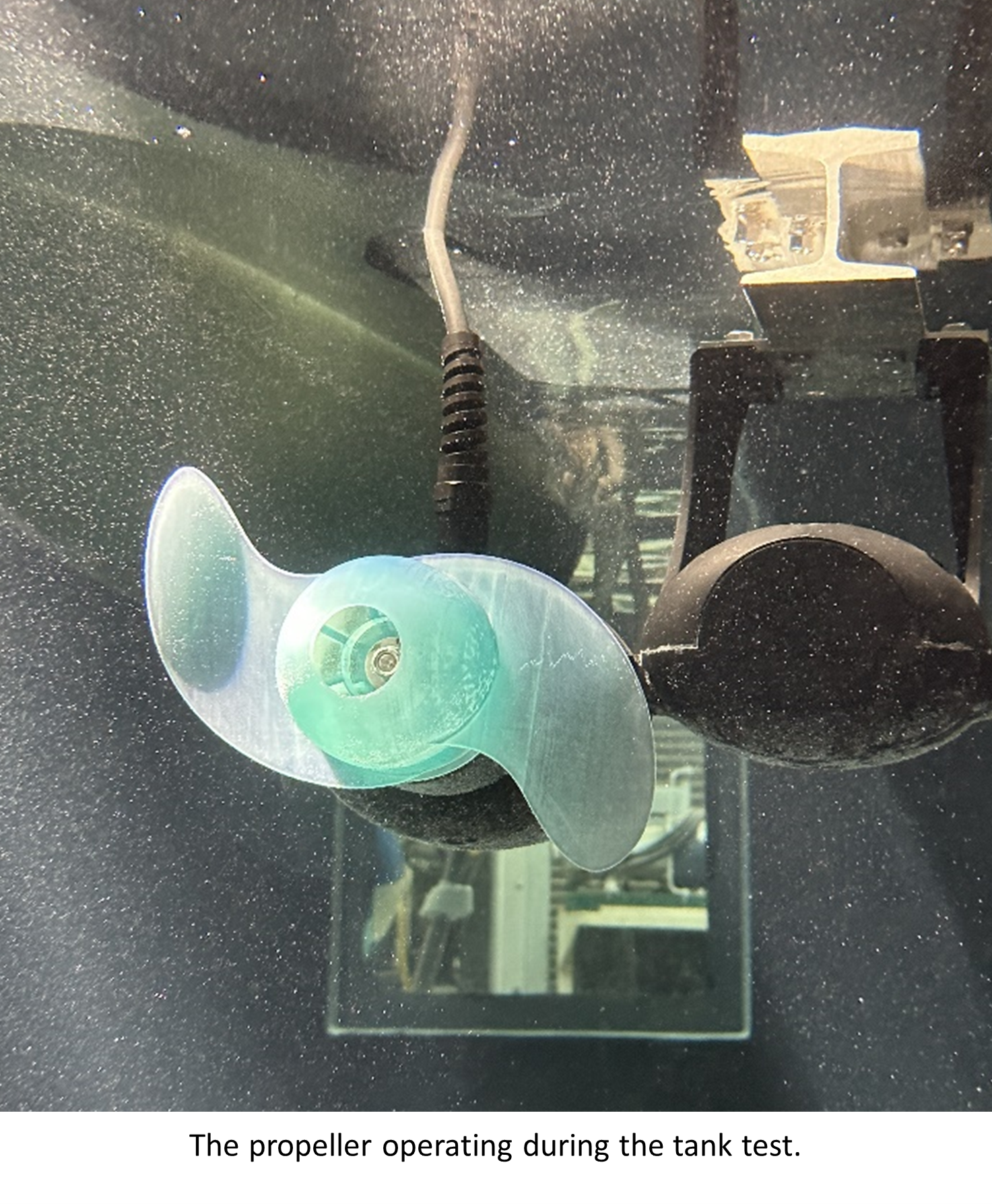
On the day of the test, we took the vehicle to the water and set up our electronics. I lightly pushed forward on the controller, ready to see the improved performance of the vehicle. Instead, one of the two new propellers immediately snapped and was lost to the bay never to be seen again. With our numerous failed attempts, we decided that printing a propeller out of resin was not a viable method of manufacturing the part. We put this portion of the project on hold and began to focus on other improvements.
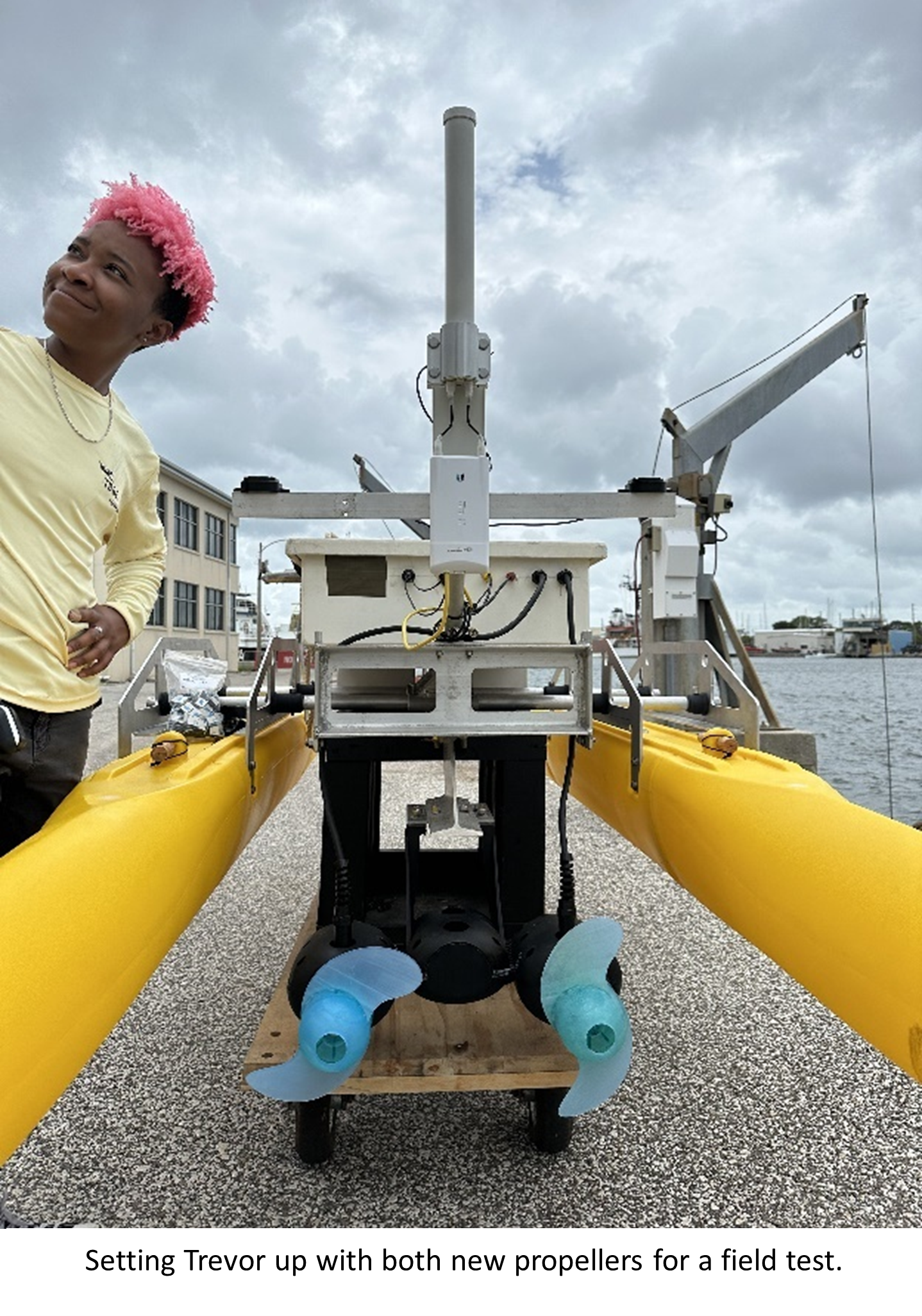
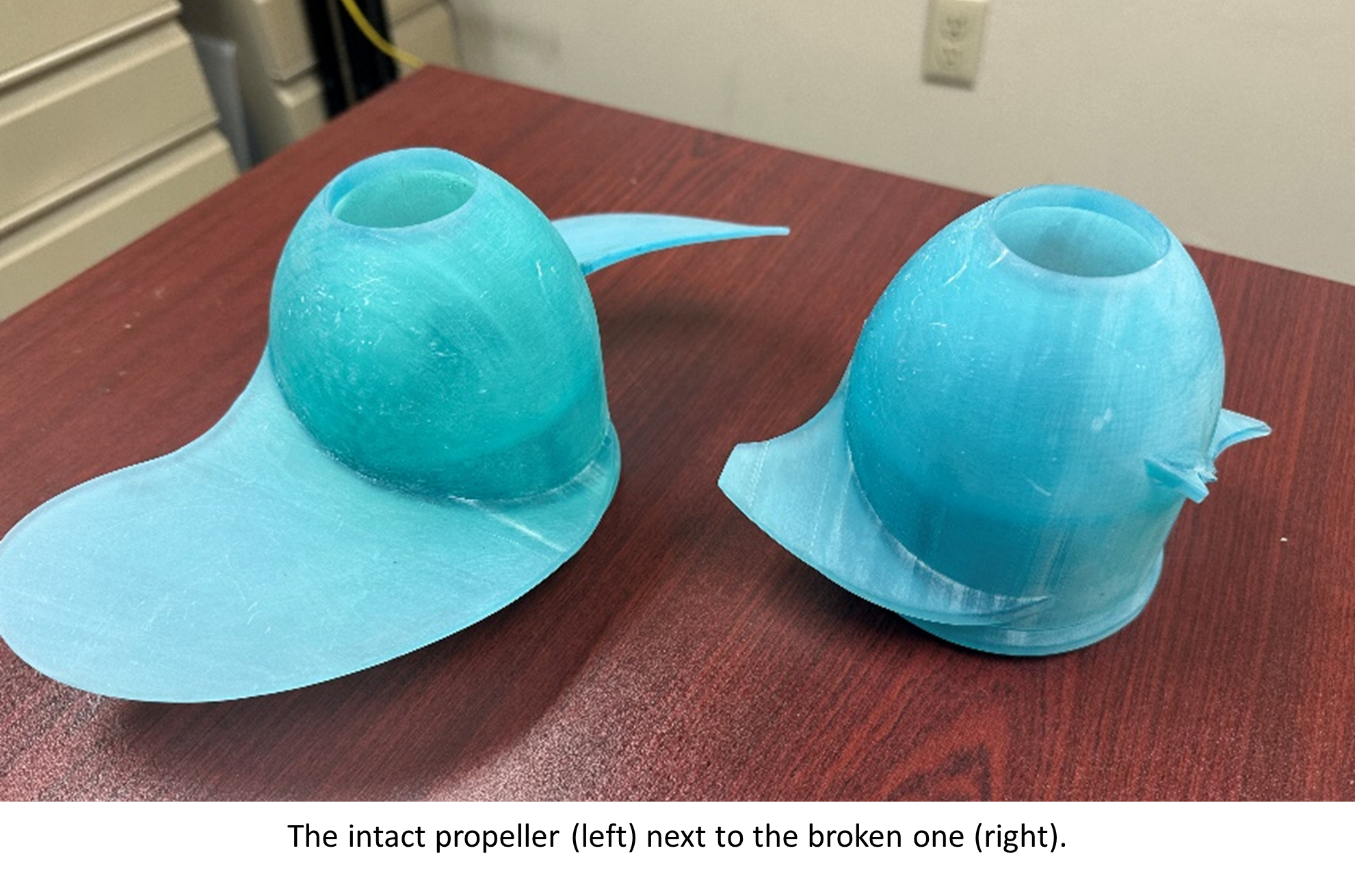
The vehicle had a lot of cavitation, or bubbling, and was making a lot more noise than it should have been during the test. Our solution was to lower the props by a few inches using a spacer. We put it back in the tank again and found that we had successfully lowered the props to a level that we were happy with.
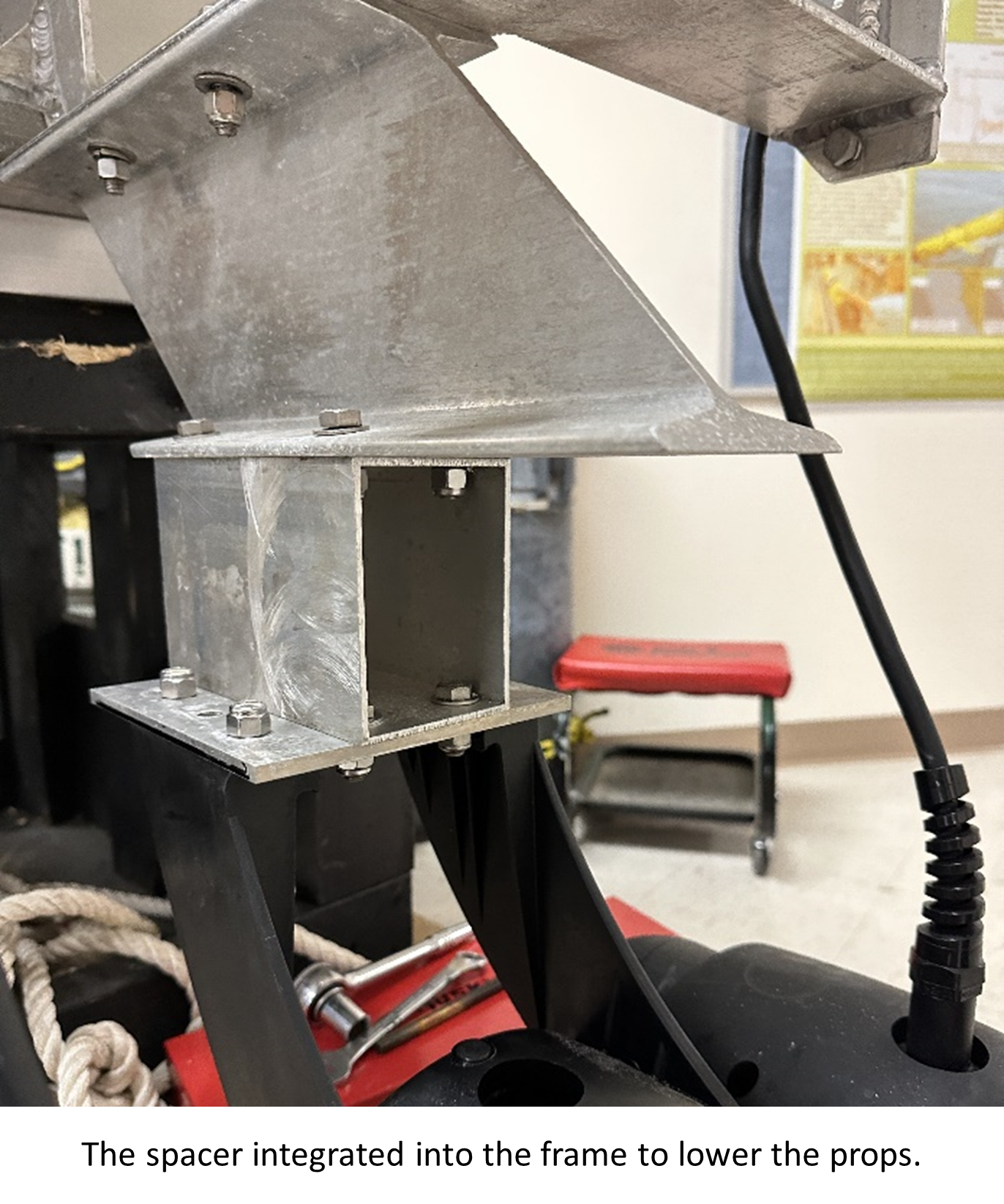
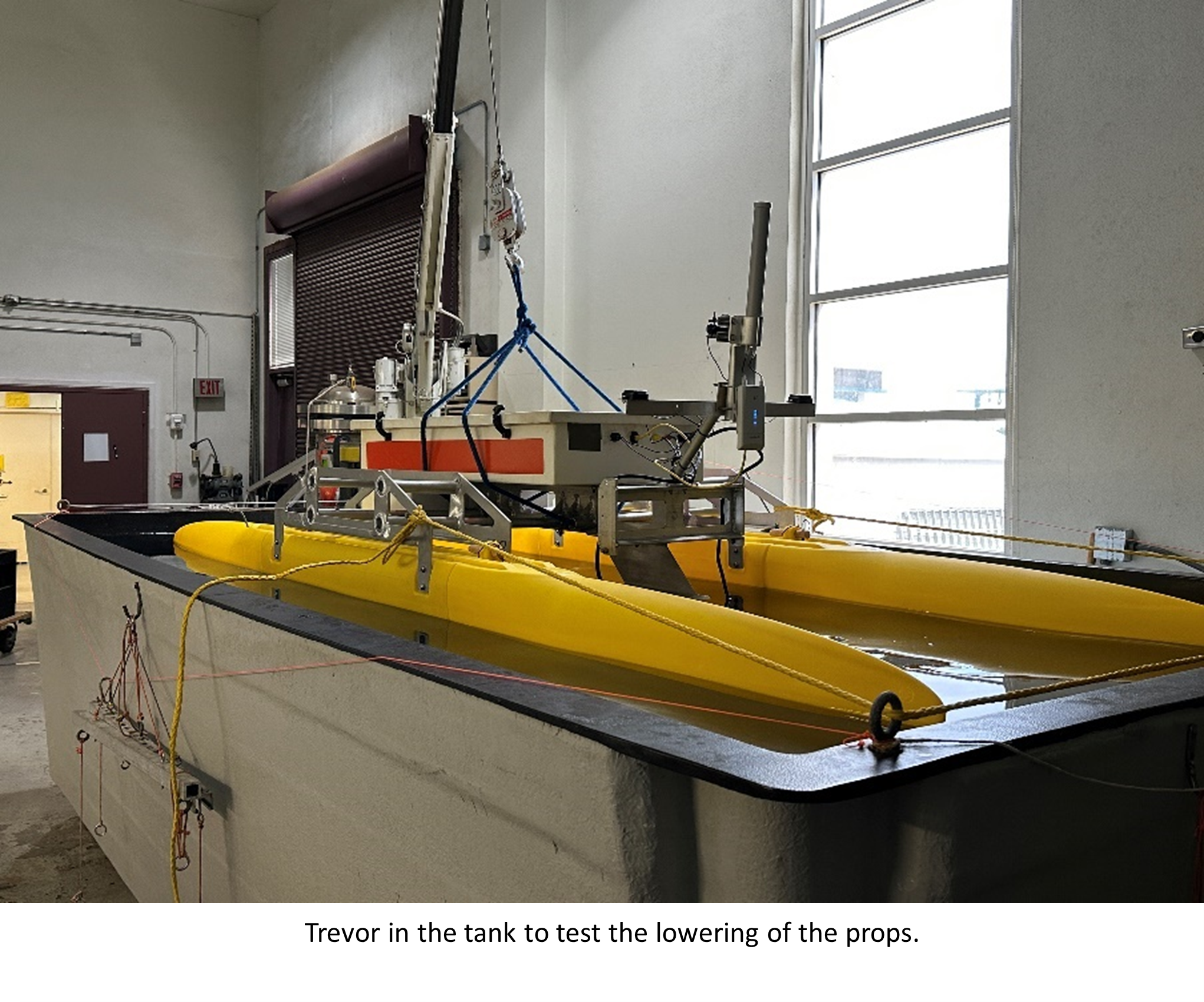
About a week later, we decided to do a field test to check how much improvement there was with the cavitation issue. By now you know what comes next. I must say that we got at least 10 minutes of problem free testing before things went south and ultimately, we broke something. This break was much less permanent than the previous ones, but it was also much more action packed than usual.
Let me set the scene. I’m up on a balcony controlling the vehicle with our wireless controller, watching it glide through the water a short distance out from the sea wall. We didn’t want to drive the vehicle out too far since we don’t know the range the connection can handle yet.
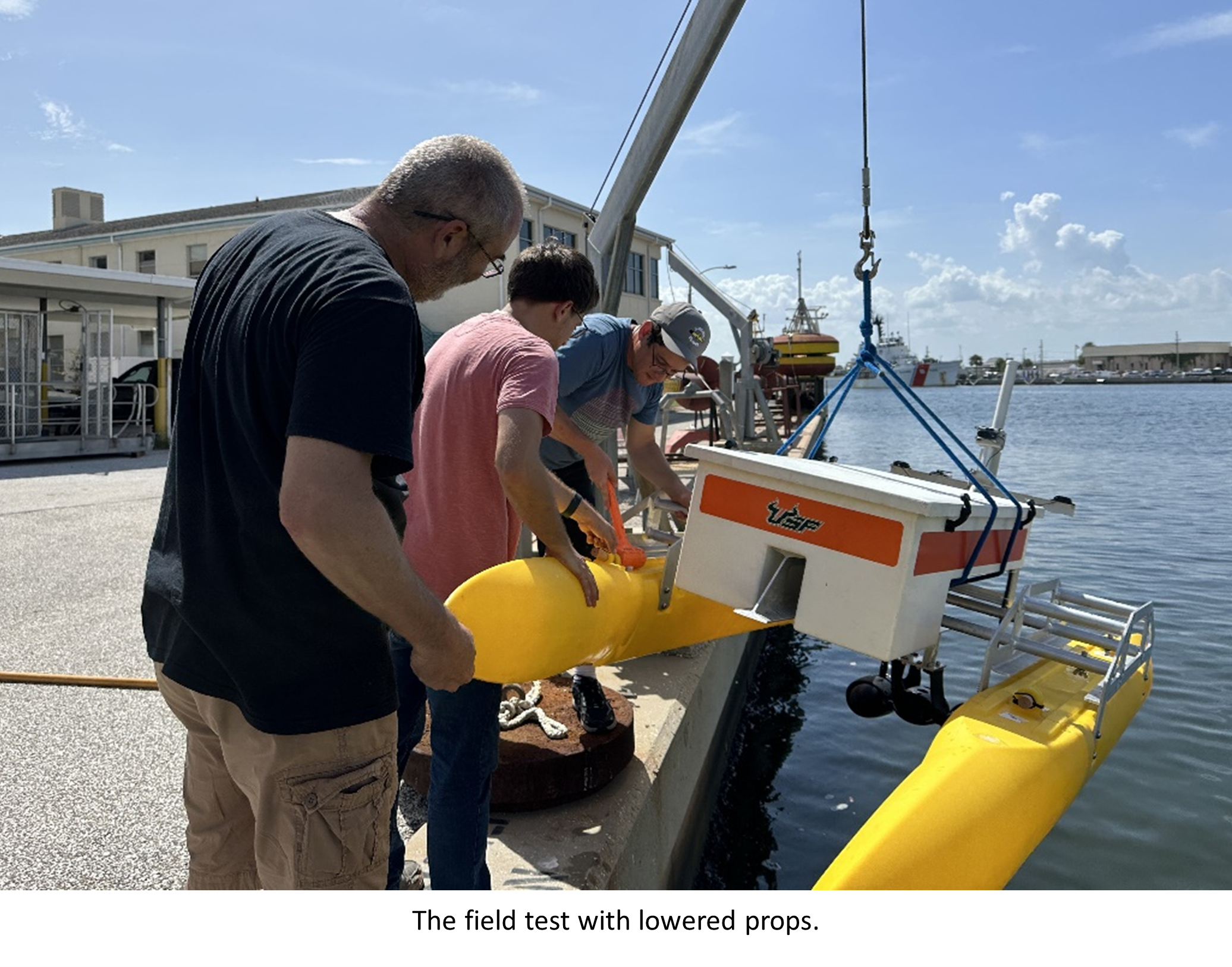
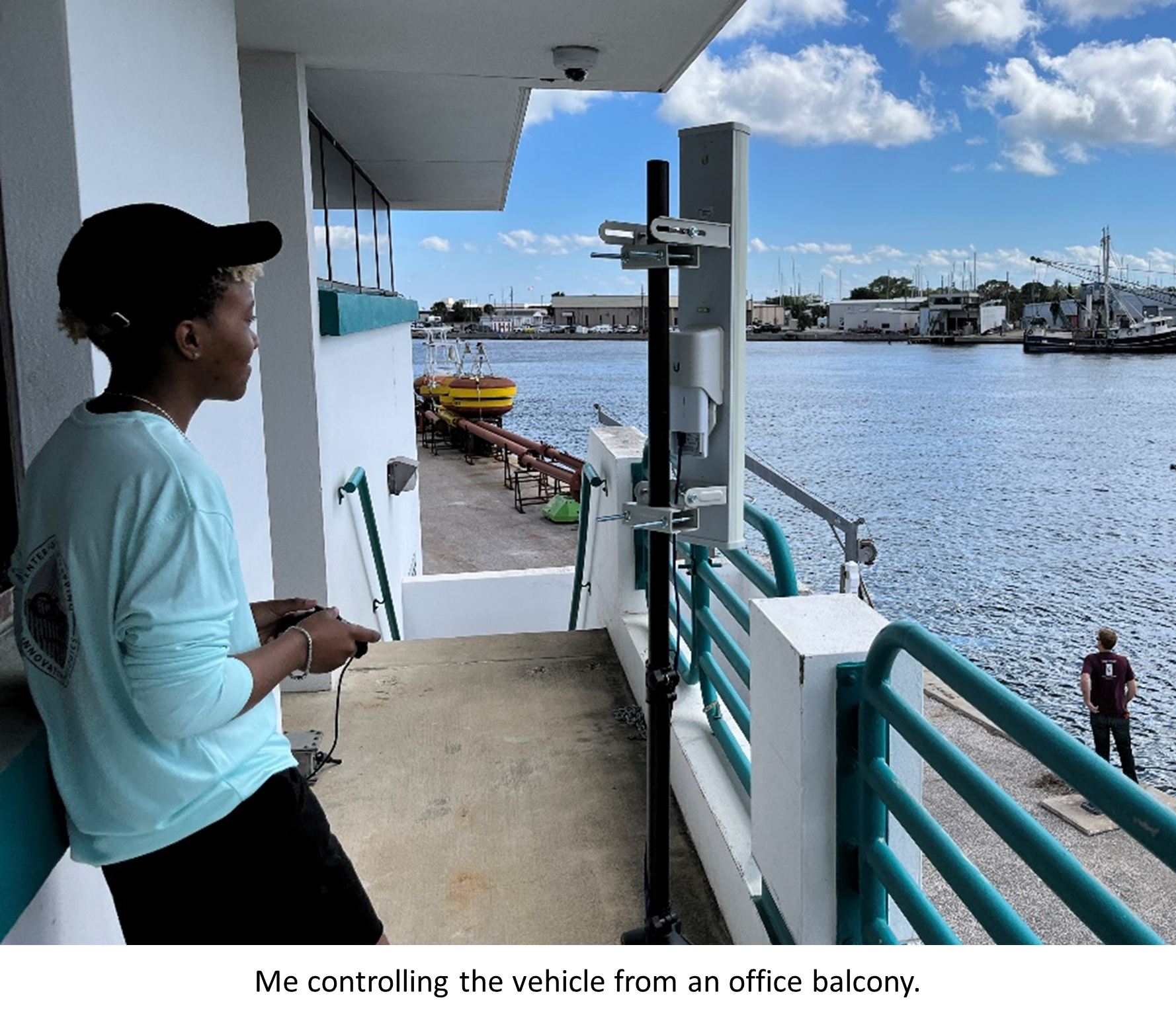
Suddenly the vehicle slows to a stop in the water despite me continuing to push on the joysticks. I yelled down to my project lead, Kris, that the controller wasn’t working, and he came up to try and help me troubleshoot. As we’re doing this, I look over to the water and see Trevor driving full speed towards the sea wall. I quickly looked at the controller to see if it was somehow jammed in a forward position, but it still wasn’t even connected to the vehicle.
I heard a thud and scraping down by the water – Trevor had crashed into the seawall. When we went to assess the damage, we saw that one of the hulls had been knocked out of place. Thankfully nothing was actually broken. There was some scrapping along the side of the hull, but at least we knew the vehicle would be able to withstand hits if necessary.
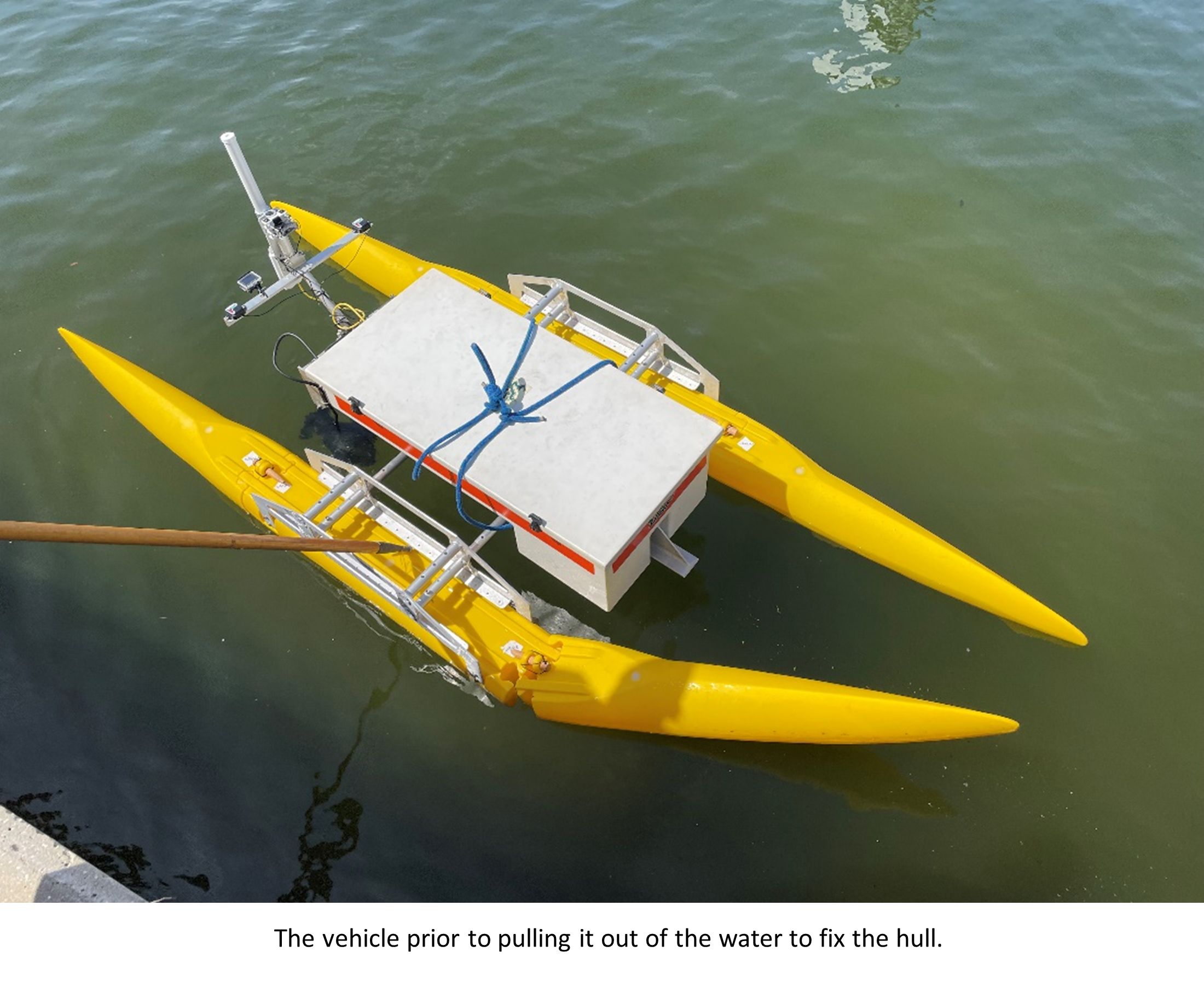
Every day that I spend here at COMIT, I learn more and more about numerous topics. In the few months I’ve been here I got to get hands-on with soldering, resin printing, manufacturing, Python, marine science, robotics operating systems and so much more. Whether you’re specifically interested in marine engineering or just trying to figure out what to do with your degree, take this piece of advice with you. Don’t limit yourself. Look at things that you have interest in, even if you don’t initially think it can be combined with your degree of choice, and research careers in the field. Chances are, you might find something that combines more than one of your interests.
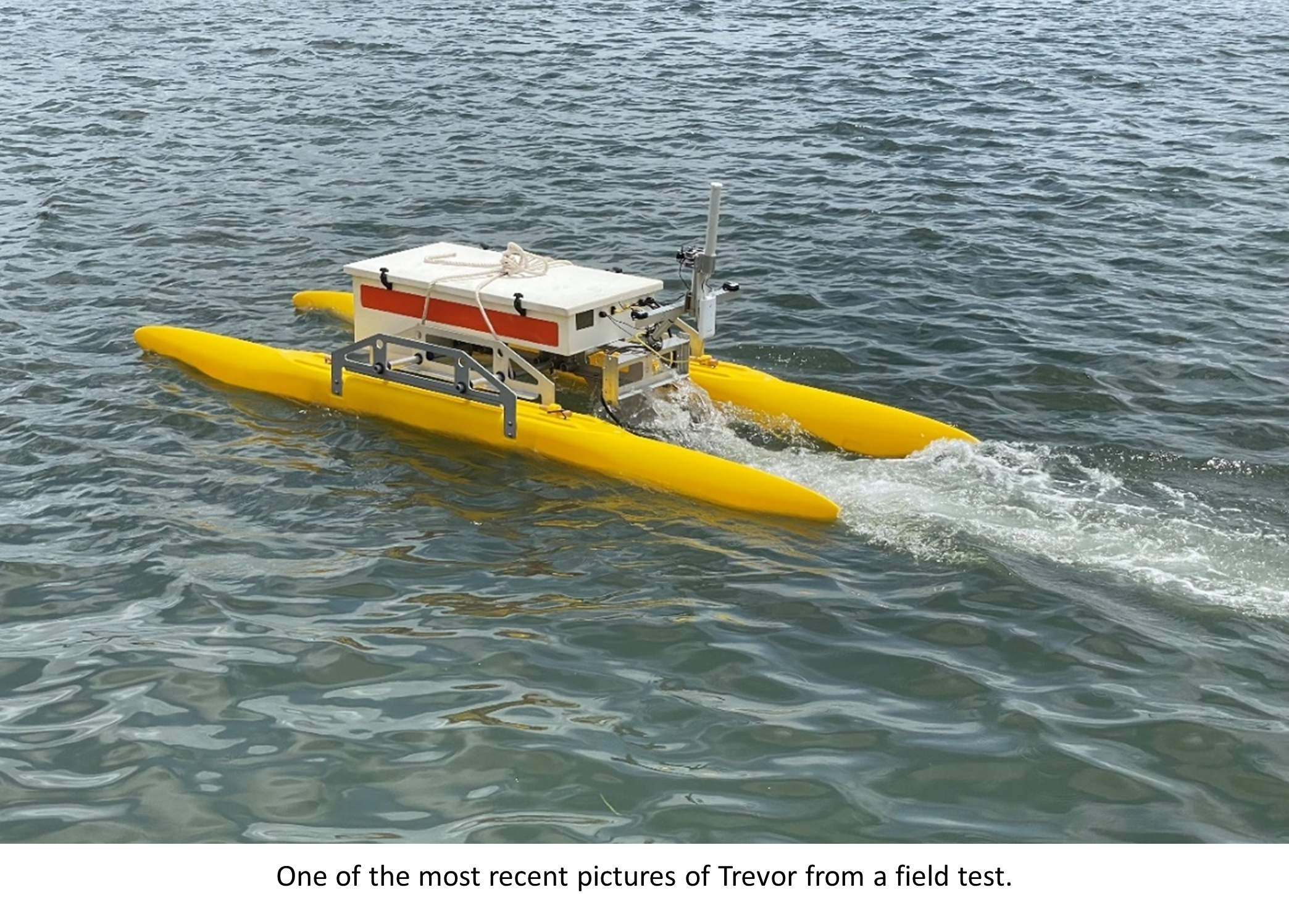
Recent Comments